Germantown, MD
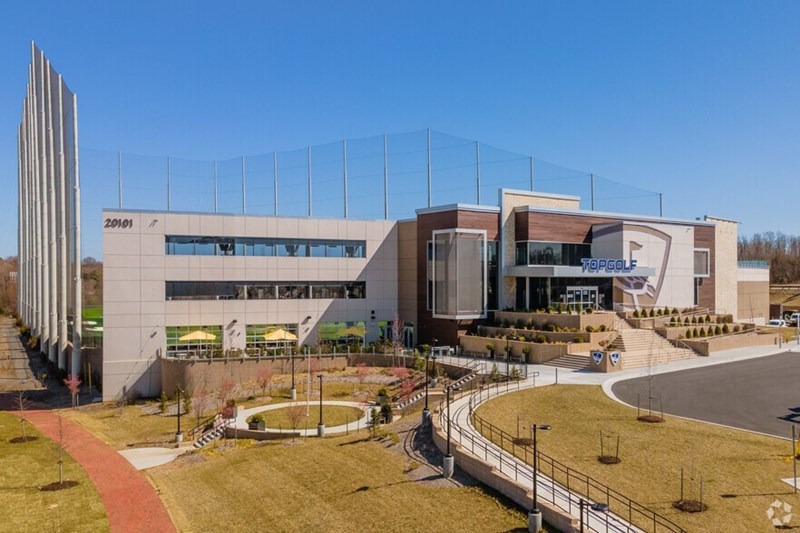
Project: Top Golf
Location: Germantown, MD
Owner: TopGolf USA
General Contractor: ARCO/Murray
Total Wall Area: 32,000 SF
Project Cost: $1.3 Million
The site location chosen for the TopGolf project in Germantown, MD presented many unique topographical challenges. As an industry leader in providing retaining wall applications, Roche Bros., Inc. (RBI), worked together with project participants to propose and execute value engineered solutions meeting the needs of the Owner and site.
To create space for the infield, building structure and parking lot, a significant “cut” retaining wall was required along the entire East portion of the site. This wall presented several challenges as the limits of excavation could not disturb the right-of-way for the MD Rte. 118 off ramp that the wall would be supporting. To further add to the difficulty of this wall, bio-retention facilities were placed directly below the tallest portion of the wall, adding to the overall height and grade required to be supported. RBI worked with Arco/Murray and Hillis-Carnes to avoid the use of a costly Post and Panel or Soil Nail system. It was determined a segmental block retaining wall would work using select aggregate backfill and staggered geogrid lengths to limit excavation depth, maintaining all permanent reinforcement within the property line.
The Western portion of the site was supported by a 20’ tall “fill” retaining wall that required considerable coordination due to the myriad utilities and storm structures located within and below the reinforced zone, and 150’ tall net-poles in front of the wall. This retaining wall also connected to the foundation of the TopGolf building structure, adding to the coordination efforts.
Additionally, RBI proposed and coordinated the design efforts to allow for installation of parking lot railings within the wall block, rather than 2’ behind the wall – helping to save critical parking space and provide safer access to clients.
Lastly, the bio-retention facilities were value engineered as segmental block walls, in-lieu of costly CIP walls, where possible—saving thousands of dollars. RBI leveraged industry experience and its professional network to provide a turn-key installation for the required project scope, subcontracting the CIP Stem Walls necessary for the interior portions of the Bio-Retention Facilities. RBI’s ability to include and deliver on out-of-scope items, coupled with our capability to dedicate the requisite manpower to meet the project schedule, separated us from other wall contractor’s being considered as the right team for the job.
This project highlighted Roche Bros., Inc.’s professional capability to provide unique, cost-effective solutions to site specific challenges, as well as the bandwidth of RBI’s workforce to operate effectively with professional organizations to manage and execute large scale retaining wall projects.